平成26年度 日本機械工具工業会賞
技術功績賞
高能率・高送りカッタ「MFH型」の開発 | 京セラ株式会社 |
石 寛久(いし ひろひさ) 山道 一輝(やまみち かずき) 眞尾 将平(まお しょうへい) |
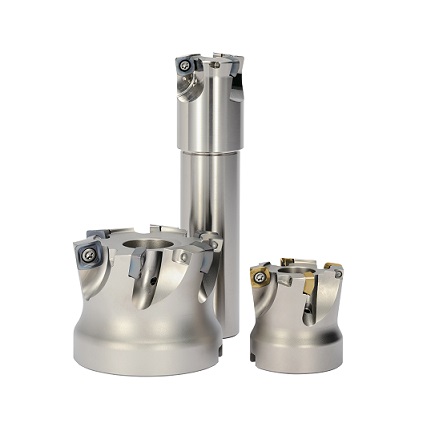
①技術の特徴
本開発品は高能率加工の実現と、多様化するユーザーニーズへの対応を目的とした高送りカッタである。高送りカッタは突き出しの長い加工で使用される場合が多く、耐ビビリ性能の向上が課題であった。MFH型では従来平面形状であったチップの切れ刃形状を3次元凸型切れ刃に改良することで、ワーク食いつき時の衝撃を抑制し、耐ビビリ性能を大幅に向上させた。
また、従来の高送りカッタは切込み量の制限により、加工環境やワークの種類によっては使いづらい場合があった。MFH型では、3タイプのチップを同じホルダに装着可能とすることで、多様な加工の要求に対応している。
②新規性/独創性
従来の高送りカッタは、チップが平面形状であるため、ワーク食いつき時の衝撃によってビビリが発生することがあった。MFH型の特長は、食いつき時の切削抵抗の急激な増大を抑制するため、3次元凸型切刃構成を採用し、大幅に耐ビビリ性能を向上させたことにある。
また、MFH型では、コンセプトが異なる3タイプのチップを、同じホルダに装着可能としたことで、最大で縦切り込み5mmの加工や、仕上げ加工といった従来の高送りカッタでは対応できなかった加工領域をカバーしている。
③協会に対する啓発度
ワーク食いつき時の衝撃を抑制する事で安定的に高能率加工が可能となり、ユーザーの生産性向上に貢献する事ができる。また、従来の高送りカッタとしての機能に加えて、切り込みが大きい領域から、仕上げ加工まで対応できるため、工具本数、非稼働時間の削減に貢献することができる。
※環境調和製品認定済
高能率マルチコーナラジアスカッタ「MRW型」の開発 | 京セラ株式会社 |
出口 慎(でぐち しん) 山本 雅大(やまもと まさひろ) 牧野 貴彦(まきの たかひこ) |
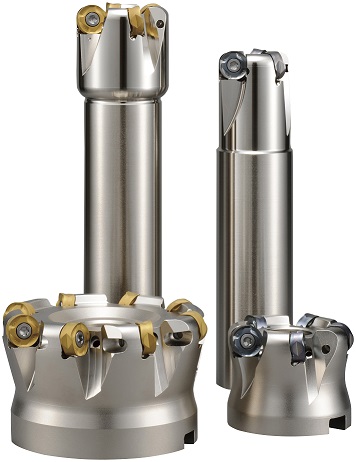
①技術の特徴
MRW型は難削材加工の生産性向上に貢献する高能率マルチコーナラジアスカッタである。
近年、エネルギー産業を中心にステンレス鋼や超耐熱合金等の難削材の使用量が増加してきている。難削材のミリング加工においては、ラジアスカッタが使用されるケースが多いが、工具寿命の改善が課題であった。MRW型は「両面8コーナー仕様」、「ヘリカル切れ刃設計」および「切り込み量に応じた最適切れ刃設計」の採用により、従来のラジアスカッタの課題を解決し、難削材加工の生産性向上に貢献する。
②新規性/独創性
MRWの特長は、切り込み量の変化で、切りくず厚みが大きく変動するラジアスカッタの特性を考慮し、下記の(a)~(c)の構成によって、耐熱合金等、難削材の生産性向上、安定加工を実現したことにある。(a)すくい面、逃げ面の3次元的に変化させることで、切り込み量に応じた切刃形状の最適化を実現した (b)「両面8コーナ仕様」+「ヘリカル切れ刃設計」を採用することで、コストパフォーマンスと低抵抗を両立させた。(c)粗粒化、均粒化により、熱伝導性を向上させ、さらに添加材の抑制によって、硬質相と結合相間に生成される脆化相を抑制した、新開発の強靭性母材を採用した。
③協会に対する啓発度
低抵抗かつ刃先強度に優れたラジアスカッターの開発により、難削材の安定、長寿命加工および高能率加工を実現することで、エネルギー産業の生産性向上に貢献した。また、両面8コーナ仕様と拘束面配置を最適化したチップ形状により、環境負荷を低減し、ユーザのランニングコスト低減にも貢献した。
※環境調和製品認定済
革新的鋼旋削加工用材種GC4325の開発 | サンドビック株式会社 |
一ノ瀬 裕介(いちのせ ゆうすけ) |
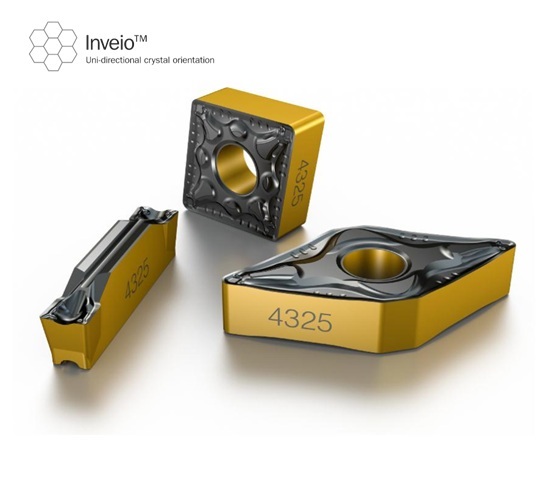
①技術の特徴
近年、切削加工業界では、様々な技術革新が起こり、高速/高能率化による生産性追求の流れが高まってきている。そうした中で、ユーザーの更なるニーズに対応するため、超硬チップの新コーティング技術「Inveio™(インヴェイオ)テクノロジー」を開発した。この技術により、チップの耐摩耗性、耐熱性が大幅に向上し、驚異のチップ寿命・加工高速化を実現。また、低速-高速条件下、軽断続-連続加工での安定した寿命を得ることに成功した。
②新規性/独創性
GC4325は、Inveio™(インヴェ イオ)テクノロジーを採用した鋼旋削加用新材種である。Inveio™(インヴェイオ)テクノロジーとは、コーティングアルミナ層の結晶成長方向を制御し て成膜する最先端技術(特許申請済み)である。結晶の最も強い面をチップの切削部に揃えることにより、高い耐摩耗性を実現。また、結晶の方向と熱伝導率の 関係を利用し、チップの切削部から熱を効率良く逃がすことで、耐熱性も向上させた。
③協会に対する啓発度
まず第一に、加工の高い再現性を持つ材種であるため、無人運転が可能となり、また、再加工の必要性も低減できる。第二に、広範囲の適用領域があ るため、工具在庫及び工具管理費の削減が可能となる。最後に、高切削条件下で長寿命なため、機械稼働率及び、生産性を向上することができる。
ハイレーキ正面フライスカッタ WGX型の開発 | 住友電工ハードメタル株式会社 |
長見 佳成(ながみ よしなり) 田淵 裕章(たぶち ひろあき) 岸 美里(きし みさと) |
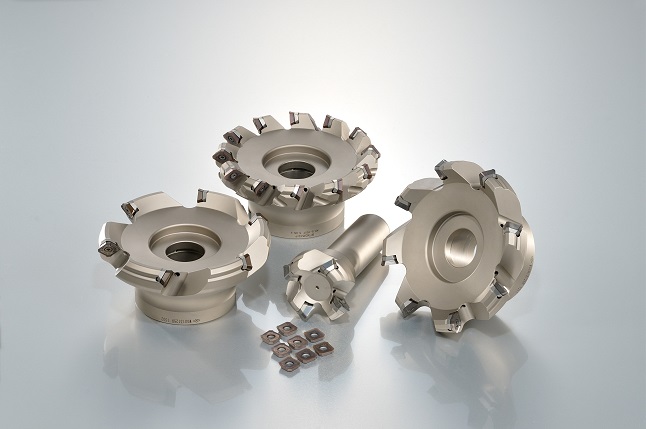
①技術の特徴
本開発製品は切り込み 角45°の正面フライス用カッタで、インサートの主切れ刃を傾けたことにより業界トップのハイレーキ設計となっており、高い切れ味(低切削抵抗)を実現し ている。そのため近年増加している小型のM/Cにおいても安定した加工が可能である。またさらい刃形状に直線刃と曲線刃を組み合わせた独自の設計を採用し ており、非常に安定した加工面品位を得ることが出来る。また無研磨チップの寸法ばらつきを抑える高精度化技術と、各種被削材に対して長寿命化が可能な最新 チップ材質のラインナップも特長である。
②新規性/独創性
従来の直線さらい刃、円弧さらい刃ではなく、両者を複合させた独自開発のさらい刃形状を採用しており、これによりチップ取付け時の微小なばらつきの影響を 受けにくくなり、安定して高品位の加工面を得ることができる。またバリ対策用チップもラインナップしており、コーナ部をチャンファ形状とし、さらにその形 状を本カッタ諸元に合わせ最適化することで、工具離脱時にワークからバリを分断させることができ、バリレス化を実現している。
③協会に対する啓発度
業界トップレベルの優れた切れ味による高い汎用性により、一般的なM/Cはもちろん、近年普及しているBT30クラスの小型M/Cでも安定して使用でき る。そのため従来以上に高能率での加工が可能となり、ユーザでの生産性、コスト削減に貢献している。また高精度なチップで刃振れを従来比1/2以下に抑制 し、前記の特殊さらい刃形状、バリ対策チップと合わせて、高品位加工をユーザに提供可能である。環境調和製品2012年度認定(2012-018)
鋳鉄加工用ストロングマルチドリルHX型の開発 | 住友電工ハードメタル株式会社 |
佐藤 佳司(さとう よしじ) 栗塚 和昌(くりづか かずまさ) 山崎 孝之(やまざき たかゆき) |
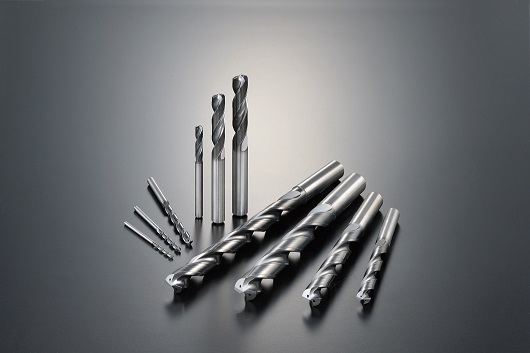
①技術の特徴
本開発はトラック、建機、工作機械産業などの大型鋳物部品穴あけの高能率化を狙ったものである。新開発のシンニング形状、刃先処理、芯厚の最適 化などにより、加工時のスラスト抵抗を大幅に低減させた。これにより、従来ドリルに対して2倍超の高送り加工を実現した。また、低抵抗化することで近年急 増している小型マシニングセンタでも高能率加工を実現できる。
②新規性/独創性
従来ストレート形状であったシンニングを円弧形状とすることで、中心部の切りくずポケットを拡大し、切削抵抗を大幅に低減させた。同時に外周の 肉厚(バックメタル)確保も可能となり、高剛性化を同時に実現している。これにより穴精度向上が可能となり、かつ加工中の振動も約30%低減した。さら に、同シンニングを採用することで、ドリル先端からサブマージンの開始位置までの距離を短くすることができ、従来ドリルよりも加工開始後により早くガイド 効果を発揮するため、一段の穴精度向上を実現している。
③協会に対する啓発度
本製品により鋳鉄の穴あけにおいて従来比2倍超の高能率(高送り)加工を実現している。さらに高送り化により同一加工長での擦過距離を軽減でき、工具寿命 延長にも寄与している。本効果により、バス、トラック、建機産業を中心とした大型鋳物部品加工の加工コスト低減に大きく貢献しており、さらに消費電力量も 低減でき環境面でも貢献が可能である。環境調和製品2014年度認定(2014-019)
難削材加工用ブレーカ EG/EF型の開発 | 住友電工ハードメタル株式会社 |
松田 直樹(まつだ なおき) 天坂 陽星(てんさか ようせい) 市原 誠(いちはら まこと) |
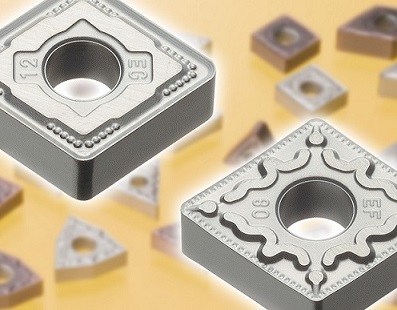
①技術の特徴
近年、難削材の需要は航空機・エネルギー機器部品などの分野で大きく伸びており、難削材用工具に対しても工具寿命延長や切りくず処理のニーズが 一層高まっている。このニーズに対応するべく、当社では難削材用の新チップブレーカラインナップとして、切りくず処理性改善はもちろんのこと、難削材加工 特有の工具損傷の抑制を狙いとしたEG/EF型を開発した。EG型ブレーカは汎用~粗切削領域で異常損傷の抑制と優れた切りくず処理を特徴とし、EF型ブ レーカは仕上げ~軽切削領域において従来ブレーカでは困難であった切りくず処理性を大幅に改善している。
②新規性/独創性
EG型ブレーカは、従来品と比べてすくい角を 大きくし、かつすくい面上に複数設置している球状突起の位置を最適化することで、切りくずカールがすくい面内で生じるようにしている。これにより難削材の 加工硬化した強固な切りくずがチップ稜線に接触して切刃外欠損が生じることを防ぎ、工具の長寿命化が可能である。EF型ブレーカは、従来品と比べて切れ味 を重視したすくい角に設定し、刃先からブレーカ壁までの距離を短くすると共に、ブレーカ壁の角度を緩やかにすることで、切りくず詰まりを防ぎながらカール 径を非常に小さくすことができ、特に切りくず処理が難しいTi合金の仕上げ加工に威力を発揮する。
③協会に対する啓発度
EG/EF型ブレーカでは大きなすくい角を有する特殊すくい面形状により、Ti合金加工などで生じやすいクレータ摩耗の進展を抑制することが可能である。 前述の切刃外欠損を含め、これら難削材特有の工具損傷を抑制し、耐熱合金・チタン合金などの長寿命加工を実現している。加えて優れた切りくず処理性により 安定した加工が可能であり、多くの難削材加工ユーザーに貢献可能である。環境調和製品2014年度認定(2014-017)
旋削加工用高耐摩耗性サーメット T1000Aの開発 | 住友電工ハードメタル株式会社 |
松田 一臣(まつだ かずおみ) 広瀬 和弘(ひろせ かずひろ) 渡部 和広(わたなべ かずひろ) |
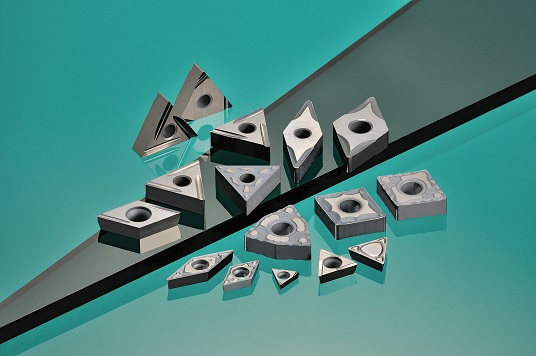
①技術の特徴
自動車や産業機械分野における加工の高能率・高精度化に伴い、被削材も多種多様となり、仕上げ工程においても汎用性の向上が求められている。特に、高硬度の被削材や鋳鉄、焼結合金などは単純な機械的摩耗だけでなく、被削材との凝着や反応摩耗などが複合し、工具の摩耗損傷がより進みやすい。同時に 凝着はチッピングや加工面悪化の原因にもなることから、耐摩耗性/耐欠損性/加工面品位トータルの向上が必要である。このような背景の下、適用被削材の汎 用性が高く、加工における寸法変化の小さい耐摩耗性に優れた新サーメット工具「T1000A」を開発した。
②新規性/独創性
一般的なサーメット工具は靱性と熱伝導率を向上させるためにタングステンを添加しているが、これにより被削材との凝着や反応が生じにくいという サーメットが持つ本来の特長が損なわれてしまう問題があった。本材種はタングステンを添加し靱性と熱伝導率を向上させながらも、最新の粉末・焼結技術によ りタングステンを硬質相中に閉じ込めることで、被削材との凝着、反応を防ぎ、加工面品位の向上および高い耐反応摩耗性を実現させた。加えてこの高靱性組織により耐欠損性を維持しながら高硬度化することが可能となり、同クラスの製品では最高レベルの硬度を持ち耐機械的摩耗性も向上している。
③協会に対する啓発度
T1000Aは市場のニーズに対応すべく、鋼に加え鋳鉄や焼結合金の分野においても、耐摩耗性のみならず耐欠損性をも向上させた材種である。また高い耐反応性により加工面品位の向上も可能である。特に、溶着しやすい被削材や摩耗しやすい高硬度被削材に対して威力を発揮する製品であり、顧客における生産性の向上や工具コスト削減に貢献するものと確信している。環境調和製品2013年度認定(2013-002)
高硬度材加工用「フィニッシュ・ハードリーマ」の開発 | ダイジェット工業株式会社 |
津曲 達也(つまがり たつや) 後藤 光利(ごとう みつとし) 坂本 正和(さかもと まさかず) |
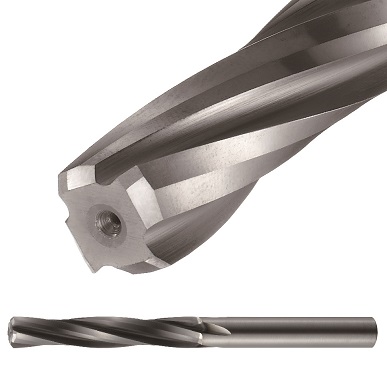
①技術の特徴
本開発は、金型加工及び部品加工業界向け高硬度材の穴仕上げ加工改善を狙ったものである。
特徴としては高硬度材の穴仕上げリーマ加工における、切れ刃欠損、リーマ本体の折損、穴精度不良、短寿命等の問題点解決目的にて、各刃先諸元を最適化し、切れ刃欠損、本体折損を抑制し且つ穴精度を向上させ、更に高硬度材加工に最適な新超硬材種を採用することにより長寿命化を実現したことにある。
②新規性/独創性
上述問題点を解決するために、すくい角、逃げ角、マージン形状、芯厚、ねじれ角、バックテーパ、食付き角を最適化し、且つ切れ刃の刃立ち性、振れ精度の向上を図った。これらの改善により、切れ刃の欠損、本体折損を抑制することができ、高い穴精度と穴公差等級 IT7 が可能となった。
更に、高硬度微粒子超硬合金母材と耐酸化性・耐欠損性に優れたPVD被膜を組み合わせた「JC6102」DHコートを採用することにより長寿命化を図った。長寿命化においては、特にマージン部分の摩耗進行を抑制することにより、再研削量を削減することが可能となり且 つ止まり穴においては、下穴ドリルの穴深さを浅くすることも可能となった。
③協会に対する啓発度
再研削量の低減の点でユーザー及び社会に対してレアメタルなど資源の節約に貢献した。長寿命化及び高精度化により、ユーザーに対して工具費と人件費の低減で貢献した。
溝入れ加工用工具 EasyCut の開発 | 株式会社タンガロイ |
佐々木 泰岳(ささき やすたけ) 坂内 由昌(ばんない よしまさ) 中林 洋介(なかばやし ようすけ) |
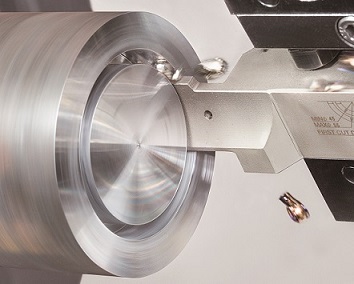
①技術の特徴
従来の溝入れ工具のセルフクランプ方式は、弾性変形を利用した上顎と下顎でインサートを挟み込む機構の為クランプ剛性が低く、横送り加工ができない問題が ある。一方ねじ止め方式では、インサート交換に時間がかかる問題がある。さらに深溝加工や端面溝入れ加工では、上顎が切りくず排出を阻害するという問題が ある。そこで本開発では、横送り加工、クイックチェンジ、深溝加工を1本の工具で可能にすることを目的とし、ポケット形状を一体型にする新セルフクランプ 方式を考案したことを特徴とする。
②新規性/独創性
開発品は、ポケット側面に壁を設け、上顎と下顎を連結することにより、クランプ剛性を高め、横送り加工を実現した。また、ポケットをテーパ穴にすること で、クイックチェンジを実現した。さらに、インサートを斜めに挿入する仕様としたことにより、切りくずポケットを広くとることができた為、スムーズな切りくず排出を実現した。
③協会に対する啓発度
EasyCutは、差し込み式の新セルフクランプ方式を採用することにより、クランプ剛性を高め、横送り加工や外径、端面深溝加工を可能にしたことから、1本の工具でのマルチ加工を可能とした。加工条件を制限せず、インサートのクイックチェンジを可能にしたことで、段取り時間を短縮し、御客様の生産性向上 を実現している。
6コーナサイドカッタ TungSlot「TSW/ASW形」の開発 | 株式会社タンガロイ |
小宮山 哲司(こみやま さとし) 黒川 正寛(くろかわ まさひろ) 松本 修(まつもと おさむ) |
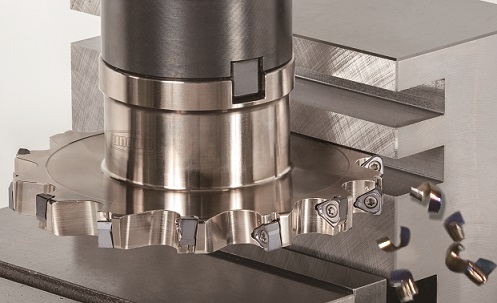
①技術の特徴
高能率加工、工具費低減が業界を問わず求められている。最適化されたチップブレーカおよび切りくずポケットにより、どのような被削材においても優れた切り くず排出性を示し、深溝であっても高能率に加工することができるサイドカッタを開発した。また、高精度インサートの採用により溝底の段差を最小限にとどめ 加工面品位を向上させた。加えて、両面仕様6コーナのインサートとすることにより、高負荷条件下での信頼性を向上させ、また、工具費を大きく低減させた。
②新規性/独創性
多コーナ化実現のため、両面仕様インサートとする場合の問題点として、抵抗増加・切りくず排出性悪化などが考えられる。これに対し、FEAを用いてチップブレーカ形状・切りくずの形状・ポケットを最適化し、低抵抗で優れた切りくず排出性を実現できた。さらに、インサート厚みを十分確保することにより、両面 仕様であっても、着座安定性とインサートの信頼性を向上させた。
③協会に対する啓発度
コーナ数を増加させるだけでなくインサートサイズも小さくし、従来品(4コーナ)と比較して超硬使用量/コーナを約65%減少させた。低抵抗化と切りくず排出性の向上により、従来複数パスで加工していた溝も1度に加工することが可能となった。また、最適化されたポケットサイズにより多刃化に成功。本工具は、大幅なコスト低減と生産性向上に貢献することができる。
雄ネジ頭部の六角穴加工用工具『Shaper Duo』の開発 | 日本特殊陶業株式会社 |
服部 恭治(はっとり きょうじ) 中野 裕亮(なかの ゆうすけ) |
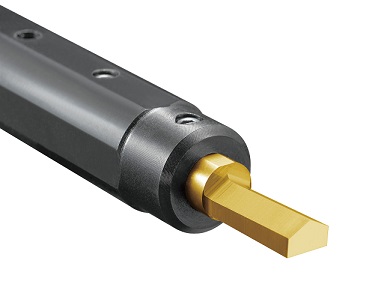
①技術の特徴
本開発は、ネジ業界向 けの雄ネジ頭部の穴加工の改善を狙ったものである。雄ネジ頭部の穴形状には、六角穴、四角穴、プラスドライバー穴、マイナスドライバー穴などの規格がある が、本製品は、Hex1.5~8までの六角穴に対応している。従来製品は、雄ネジの軸部をネジ切り加工した後、別工程にて頭部の穴加工を実施していたが、本製品は、小型自動旋盤にて軸部を加工した直後に頭部の穴加工を実施できるように改良した点に特徴がある。
②新規性/独創性
従来、雄ネジ頭部の穴 加工は、熱間鍛造やプレス加工、および、放電加工などが用いられる事が多かったが、いずれも軸部の加工後に一度自動盤から取り出して、別工程(別の加工 機)にて実施しなければならない問題があった。本製品は、小型自動旋盤にて軸部の加工を実施した直後に工具を変更するだけで、雄ネジの頭部に六角穴を加工 できるようにしたことに新規性がある。
③協会に対する啓発度
鍛造工程、プレス工程を切削工程に変更できるので、切削加工業界の市場を僅かながらでも拡大できる点において、協会員に対し新しい観点を提供した。また、ネジ業界での工数低減、コスト削減にも貢献した。
高硬度鋼小径深穴加工用工具の開発 | 日立ツール株式会社 |
吉岡 尚吾(よしおか しょうご) 佐藤 亮介(さとう りょうすけ) 吉村 彰(よしむら あきら) |
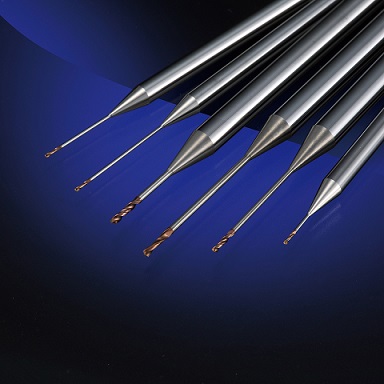
①技術の特徴
近年、金型の長寿命化に伴い被削材の高硬度化が進んでいるが、高硬度鋼を加工できる穴あけ工具は少ない。特に穴深さが工具直径の10倍を超える深穴を加工できる工具は少なく、実際の加工用途において満足頂けていないのが現状である。今回開発したエポックマイクロステップボーラーHは、50HRCを超える高硬度鋼に、工具直径の30倍までの深穴を加工できる工具であり、工具直径は0.1mmから2.0mmまでラインナップしている。
②新規性/独創性
当社では小径深穴加工用工具としてエポックマイクロステップボーラーSを以前より発売しているが、50HRCを越える高硬度鋼の加工では、切削初期においてチッピングが発生し安定した加工が困難であった。そこで、本工具においては高硬度鋼の加工においてもチッピングせずに、安定して切り屑が排出できる独自の刃形形状を開発し採用した。
③協会に対する啓発度
高硬度鋼の加工においては従来は穴あけ加工を放電加工で行っており、段取り工数、加工時間が長い等の課題があった。今回開発した工具は、当社オリジナルの高硬度鋼用インサート工具、エンドミル、ねじ切り工具等と組み合わせて使うことで、全て切削加工にてブロック材から金型を製造可能とするものである。これにより金型製造期間の短縮へ大きく寄与できるものである。
ガイドパット付往復切削仕上げ工具の開発 | 富士精工株式会社 |
岩堀 敦志(いわほり あつし) |
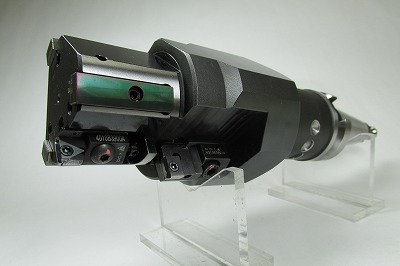
①技術の特徴
本製品は、ミッション ケースなどのアルミ部品加工において粗工程と仕上工程を集約し、一発で加工できる「工具費の低減と加工時間の短縮」を実現させることを目的としたボーリングツールである。往復切削仕上げは、切削抵抗によるツールの変位を利用した往路加工を行なった後、ツールが原位置に戻り、変位分の微小取代を「引き切削」により仕上げる(復路加工)ことを特徴としている。その際、ツールのたわみ過ぎや振動を発生させ易いという問題点は、ガイドパットを付加する事で抑制している。
②新規性/独創性
従来、粗工程と仕上工程で各1本のツールが必要であったが、一発加工の採用により本製品1本で仕上げ加工が可能となった。また復路の仕上げ加工は微小切削で低負荷である為、ワークの形状や各部剛性による加工精度への影響が少なく、高精度加工を可能にした。本製品はツール本数の削減や工具交換(ATC)時間の削減、製品精度の向上に寄与している。
③協会に対する啓発度
「工具費の低減」と「加工時間の短縮」は多くのユーザーにとって重要な取り組み案件であり、その両方を実現可能にする本製品には大きな期待がある。この加工対象を広げていくことでユーザーの生産性向上に大きく貢献できる可能性がある。
超硬ソリッドドリル MVE/MVS形 | 三菱マテリアル株式会社 |
山本 匡(やまもと ただし) 田渕 貴仁(たぶち たかひと) |
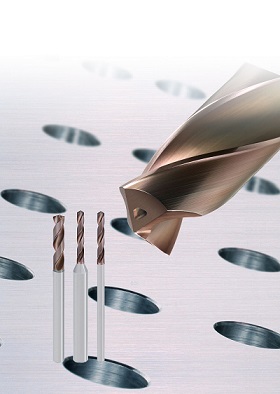
①技術の特徴
用途の広い汎用ドリル において、より高能率/長寿命を図り、加工コストの低減を可能とする製品を、顧客に提供することを目的とする。従来の切れ味(低抵抗)を維持し、切刃強度/耐欠損性を更に向上させた切刃形状を有する。クーラント穴形状を略三角形とすることで、従来品(丸穴形状)と比し、工具剛性を損なわずに、クーラント量 を増やすことができ、切屑排出性の向上、工具寿命の延長が図られる。コーティング膜は、耐酸化性および耐摩耗性に優れた(Al、Ti、Cr)N系の積層 コーティングにより、従来の1.5倍の長寿命、特に炭素鋼における工具寿命の改善に優れている。
②新規性/独創性
コーティング膜におい て、組成を従来より多元素化することにより、耐酸化性および耐摩耗性を大幅に改善した。膜構成を多層化することで、且つ、積層数を最適化することで、膜内に生じる微細クラックの伝播を抑制し、工具寿命の改善(延長)を図ることができた。(超硬母材の、コーティング膜剥離に起因するチッピングを抑制する。) ※従来は単層膜
③協会に対する啓発度
汎用ドリルでありながら、高能率・高精度な加工を実現し(加工時間の短縮、工程集約が図られ)、省資源・省エネルギーといった、地球環境保護に貢献している。
PVDミーリング材種「MP61/71/91シリーズ」の開発 | 三菱マテリアル株式会社 |
風見 大介(かざみ だいすけ) 淺沼 英利(あさぬま ひでとし) |
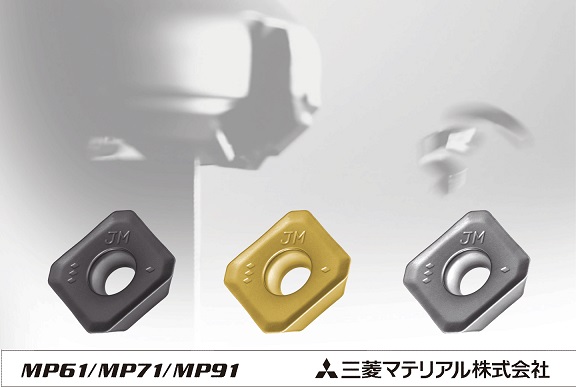
①技術の特徴
鋼、ステンレス鋼および耐熱合金・チタン合金の高能率ミーリング加工を目的とし、それぞれの被削材に対する損傷状態および損傷進展メカニズムを精査し、3種の被削材別専用新コーティングを開発した。これらと専用超硬母材とを組み合わせた鋼用材種「MP6120/6130」、ステンレス鋼用材種「MP7130/7140」、耐熱合金・チタン合金用材種「MP9120/9130」によってミーリング加工における大幅なインサートの長寿命化を実現させた。
②新規性/独創性
新コーティングはベー ス層として高Al-(Al,Ti)Nを採用。これは従来と比較して高Al量でも高硬度相(立方晶)を維持することができ、さらなる高硬度化による耐摩耗性 向上を実現した。また、各種被削材に要求される特性から最適膜種を選択し、ベース層との積層化により更なる高性能付与を実現。これらの特性は積層化によるクラック進展の抑止効果と相俟って、長寿命化に大きく寄与している。※環境調和製品認定済 MP6120/6130(認定番号:2014-003)
③協会に対する啓発度
「MP61/71 /91シリーズ」(計6材種)は被削材別に最適化された3種のコーティングと、耐摩耗性および耐欠損性に優れた専用母材との組合せにより、鋼、ステンレス鋼、耐熱・チタン合金いずれにおいても加工能率向上および工具寿命の延長を実現可能とした。これにより工作機械の稼働時間短縮、使用電力の削減、使用工具数の削減を実現し、ユーザーの環境負荷低減に寄与できる。
ヘッド交換式エンドミル iMXシリーズの開発 | 三菱マテリアル株式会社 |
阿部 太郎(あべ たろう) 畔上 貴行(あぜがみ たかゆき) |
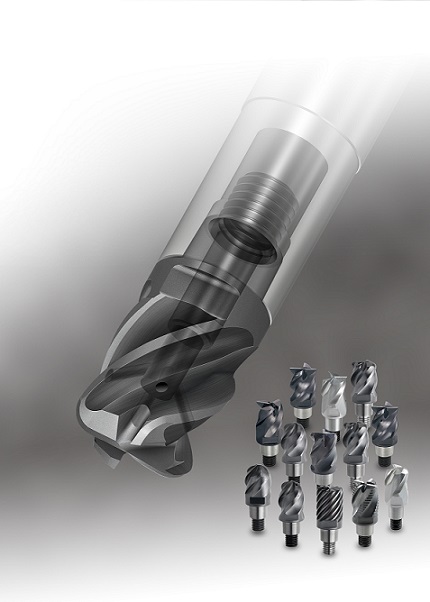
①技術の特徴
iMXシリーズは、ヘッド交換式エンドミル分野で、よりソリッドエンドミルに近い性能を狙った製品である。従来のヘッド交換式は、超硬ホルダのろう付け部に起因する剛性や強度の低下、ヘッド超硬ねじ部の破損といった問題があった。こうした問題を解決するためiMXシリーズは、「一体式超硬ホルダによる超硬ヘッドと超硬ホルダの2面拘束」および「超硬に特殊接合した鋼製ねじ」を採用した。
②新規性/独創性
超硬の2面拘束を実現するには、テーパ面の接触圧力を確保したうえで、ホルダーの引張り応力を抑制しなければならない。一方ヤング率が高い超硬で実現させるには、テーパ面角度と外径公差が非常に狭くなり、超高精度な加工が必要となる。加えて、超硬穴に高硬度鋼製のねじを塑性変形を利用して接合させることで、低コストかつ安定した高強度の異材種接合を実現させた。
③協会に対する啓発度
上記の新開発締結機構により、iMXエンドミルでは従来品よりもソリッドエンドミルに近い高精度、高能率加工が可能となり、航空機部品、金型加工などにおける精度改善、能率改善に貢献した。また、豊富なシリーズ展開により、ソリッドエンドミルからの置き換えがより広範囲で可能となり、工具費低減や環境負荷低減にも貢献した。環境調和製品認定:2013-020
超硬加工用ダイヤコートエンドミルUDCBFの開発 | ユニオンツール株式会社 |
渡邉 英人(わたなべ ひでひと) 大崎 英樹(おおさき ひでき) 大堀 鉄太郎(おおほり てつたろう) |
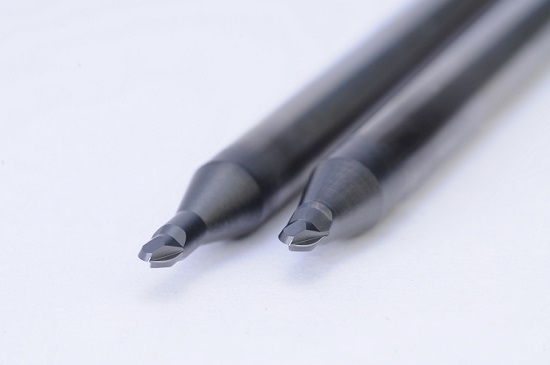
①技術の特徴
当社は2012年に 「超硬合金を切削できるダイヤコート(UDC)エンドミル」を開発した。今回の開発製品は'12年の製品に対して工具寿命と加工品位を大幅に向上させたものである。UDCシリーズの製品化によりダイス鋼やハイス鋼などと同じように超硬合金を直彫りできるようにはなったが、工具寿命や加工品位の面で必ずしも十分満足できるものではなかった。今回、'12年の製品に対して刃形状とダイヤコートを改良し寿命延長を達成した。さらに、刃先への特殊処理を付加することにより被削材エッジ部のコバ欠けを抑制しつつ均一な仕上げ面性状を得ることが可能となった。
②新規性/独創性
従来のUDCシリーズは、超硬合金を数百μmの切込みで高能率かつ高精度に加工できる反面、一般的な鋼材向け工具と比較して工具寿命が短いという課題と、被削材にコバ欠けが生じたり仕上げ面性状が不均一になる場合があるなどの加工品位の課題があった。今回、刃形状とダイヤコートを改良し、耐摩耗性を高め、従来比で約3倍の工具寿命を達成した。また、独自に開発した刃先への特殊処理工法を用いて切れ刃をシャープにすることで、被削材のコバ欠けや仕上面性状の不均一性を抑制することができた。
③協会に対する啓発度
今回の工具寿命延長により、超硬合金の直彫りを工業的に現実的なものとした。また、刃先への特殊処理により被削材エッジ部のコバ欠けを抑制しつつ均一な仕上げ面が実現できた。これらの効果により、製法を放電加工から切削加工に置き換えることが可能となり、超硬合金金型の高精度化・低コスト化・短納期化が図れるとともに、超硬合金金型の適用分野拡大につながるものと期待している。また、放電加工に比べて被削材除去に必要なエネルギーを大幅に低減できるので、環境面(省エネ)でも効果がある。